Virtual design and construction (VDC) and building information modeling (BIM) often conjure up a lot of questions. Chief among them: What’s the difference between the two?
At a high level, it’s quite simple––VDC is the overarching process, or multi-disciplinary performance model, in which BIM can be utilized as one of the tools. But VDC does not have to incorporate building information modeling and BIM can be used without being part of a VDC process.
So, what exactly is BIM? When is VDC used? When is BIM used? Are they worth the investment?
To clear up the confusion, let’s break down what each is, how they can be applied throughout a building’s life cycle and some of the primary benefits of each. But first, let’s clear up some misconceptions.
Misconceptions surrounding VDC and BIM
One of the most common misconceptions is that VDC and BIM are analogous terms that can be used interchangeably. While they are closely related when talking about infusing technology into the design/build process, they are not the same.
Another misconception is that BIM is just 3d CAD. While BIM is a 3d digital model, it’s much more sophisticated and data rich than a typical CAD model. It typically includes specific dimensional data and “families” of information about modeled elements.
Finally, the benefits of having a BIM of the structure extend well beyond the design and construction phases. It can be used throughout the life cycle of the building asset for renovation, documentation, security planning, space management, maintenance, etc. To see how it can be used throughout a building’s life cycle, let’s break down BIM further.
What is BIM?
Building information modeling refers to a highly accurate, digital representation of the physical characteristics of a building or structure. BIM is most commonly used to understand the current details of an existing structure or to design a new structure. But the benefits of BIM extend well beyond the 3d model. It enables deep collaboration and drives efficiency that allows all stakeholders––architects, contractors, engineers and owners––to work collaboratively, in real time when it is shared.
A BIM can also incorporate 4d (schedule), 5d (cost), 6d (sustainability), and 7d (facility management applications). Thus, when it is used as a true planning, coordination and collaboration tool, BIM can reduce rework, and material and labor costs, and support advanced clash detection and off-site prefabrication.
BIM can also be used to create in a virtual world to better understand relationships between spaces, materials, and various systems within a physical structure, and how actual elements will impact a structure. Virtual models can then be used for training, marketing and maintenance purposes, to name a few.
So, how exactly does VDC differ?
What is VDC?
VDC is the larger overarching methodology that often uses a BIM to plan construction. VDC is an overall process that might include various construction technologies such as pre-fabrication, advanced clash detection, visualization, scheduling, remote design, etc.
VDC processes can help mitigate design or building issues early because they are virtually constructed before any work actually begins. Once construction begins, VDC processes can be used to efficiently manage scheduling, fabrication, design changes, and advanced visualization. This improves accountability, prevents rework, and reduces waste.
Where a BIM would contain this information, VDC is the process by which technology (which may include BIM) is used to coordinate all of it.
VDC and BIM throughout a building’s life cycle
As mentioned, VDC can extend well beyond the building design phase. In fact, it's tremendously valuable during construction execution as it can be used to maintain accuracy and adherence to plans, and support collaboration and accountability across all stakeholders. For instance, as various phases of construction are completed, as-built data can be compared to the design model to check for errors/omissions and determine how it might impact future phases. If needed, it can be caught and corrected before it becomes a major issue.
BIM can also be used throughout the entirety of a building. For example, facilities management teams can use the BIM to manage building maintenance and records, discover potential issues before they become major problems, and better understand how the building is being used for energy efficiency purposes or space utilization.
It’s also advantageous for owners and architects who manage a portfolio of properties spread throughout various regions as BIM makes it possible to tour these facilities without physically being there––making them useful for management, marketing and sales. BIM technology also makes dimensional data easily accessible for planning or future renovations.
The hidden benefits of VDC and BIM
We’ve mentioned some of the core benefits of using VDC and BIM throughout the construction and building management process:
- Efficiency
- Pre-fabrication
- Collaboration
- Reduced rework
- QA/QC
- Reduced materials cost
- Reduced labor expense
But there are a few other tremendous benefits that are often overlooked. One major advantage is enhanced safety. VDC can be used to reduce the number of worker hours spent on a site and coordinate schedules to maximize efficiency when on-site labor is required. This can significantly reduce the likelihood of an incident and improve safety performance.
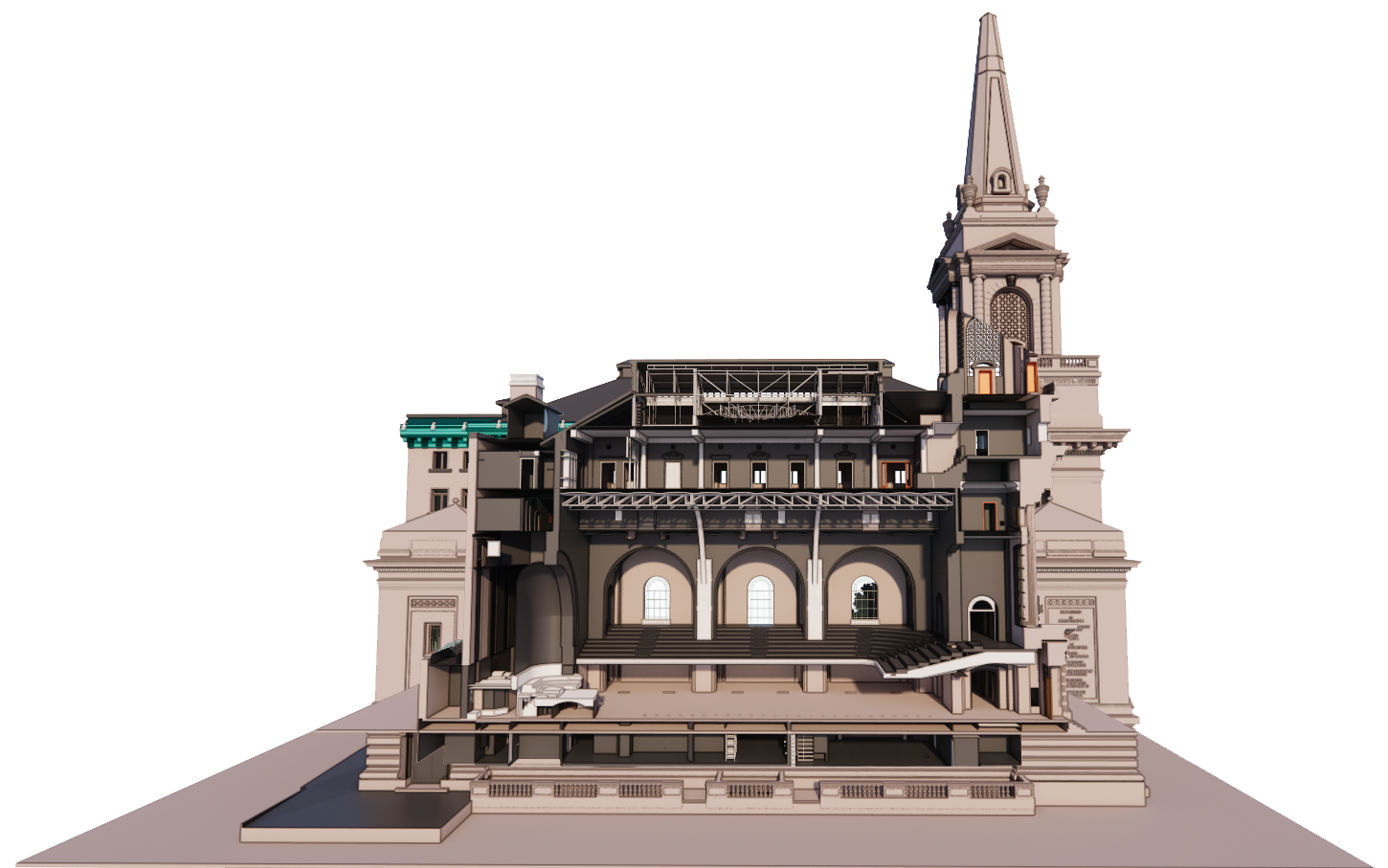
VDC and BIM can also be used to reduce the carbon footprint of a new build or existing building. For instance, forward-thinking design-build teams are using digital twins for simulation and energy modeling to reduce loads and identify electrification opportunities.
From an overall sustainability standpoint, using VDC enables teams to track the embodied carbon of the entire building––from the sourcing of the raw materials to the installation. Collecting this data at the start then becomes useful over the course of the building’s life cycle. When it comes time for renovation or adapting the space for a new use, having an understanding of the exact materials in that building makes it easier to pinpoint opportunities for reuse or recycling.
As more building owners pursue certifications like LEED, WELL, or BREEAM for their existing buildings, BIM technology––through the use of digital twins––becomes an invaluable asset. It provides a foundation and deep understanding of what you’re starting with––from the HVAC to the plumbing to the materials used. With that insight, design and construction teams can pinpoint what needs to be updated to meet the certification standards.
After construction has completed, owners and facility management teams responsible for maintaining building performance will need to be educated about the sustainable products, materials and equipment used and how to maintain them. VDC processes and BIM can be used to create a maintenance system. For instance, in the BIM model, products and materials can be tagged with relevant data sheets, maintenance requirement schedules and links for reordering. This helps ensure the building maintains performance standards, and brings organization and efficiency to the recertification and documentation submittal process––in the case of programs like LEED, WELL, or BREEAM.
Finally, for those now responsible for environmental, social and governance (ESG) reporting, building performance and even buildout are becoming important metrics. VDC and BIM will prove instrumental to accurate and efficient reporting.
Beyond the many benefits BIM and VDC produce, there are some important steps to take to get the most out of the investment.
How to get the most out of VDC and BIM investments
One of the most important steps in realizing the greatest return on your VDC or BIM investments is to determine the project goals. Various stakeholders will have different objectives. For owners, it may be risk management or to reduce costs. For construction companies, it might be schedule compression and safety. And for designers, the goal could be to understand site conditions before conceptualizing a design. But the more alignment that can occur in advance the greater value in applying technology to the build process.
Knowing the VDC mission for the project and how each stakeholder group will use this information will determine the level of detail (LOD) required. Often there will be different requirements of the BIM for each stakeholder, making collaboration from the start crucial to the success of any VDC or BIM endeavor.
The other important piece of the ROI puzzle is aligning with the right VDC consulting and execution partner. The following are just a few criteria to evaluate potential partners:
- Collaboration –– how does their team work together? Do they act as one team or is it fragmented and siloed?
- Communication –– are they timely and transparent with their communications?
- Accountability –– are they deadline driven? How do they respond if they make an error?
- Innovation –– are they forward thinking? Do they invest in the latest technology and innovation?
- Experience — does the team have the proper experience to meet the project objectives?
To gauge how they work with clients, ask for case studies or to talk to previous clients, evaluate how quickly they respond and their attention to detail in those responses, and evaluate how willing they are to provide guidance and education throughout the process. There’s more on this topic in our blog post “How to evaluate potential VDC consulting and execution partners”.
As our world rapidly evolves, technology enables us to keep pace. Sustainability, ESG, construction site safety, and adaptive reuse will only continue to become more urgent priorities in this industry. And VDC and BIM provide pathways to meet those needs. But as this technology progresses, it can often create more questions. Don’t be afraid to lean on trusted VDC partners. Ask questions. Get curious. This technology can no longer be ignored.