Rework has devastating effects on the cost and schedule of a project, with an average of 2-20% of a given project’s contract value going toward rework. And the time overruns are worse, at roughly 7-12% of total work hours.
The unfortunate reality of the construction industry is that nearly every project faces some type of rework, whether it’s due to poor design models, field changes, or miscommunication. Traditional construction drawings involve a lot of manual work which often results in irregularities and poor coordination across the various disciplines. And the likelihood that there are “clashes” between materials that are installed by different trades makes the situation more costly.
While rework in construction is prevalent, there’s a growing consensus that it can be significantly mitigated. That’s why many firms are making a conscious effort to avoid this cost inflating issue by implementing Building Information Modeling (BIM) and an overall Virtual Design and Construction (VDC) process that significantly reduces risk. These processes involve the use of 3D technology, pre-planning, pre-fabrication, and advanced clash detection to name a few.
Delivering a high-quality facility in ahead of schedule
In developing a site for an e-commerce company in the Las Vegas metro area, our client was tasked with delivering a 650,000-square-foot, cross-dock facility, where materials are unloaded from incoming semi-trucks and loaded directly onto outbound trucks with little or no storage between.
The challenge was to deliver a high-quality facility that met client and tenant expectations while adhering to a very aggressive timeline. At the same time, our client needed to reduce spend on reconciling clashes in the field — clashes with the potential to amass change orders totaling hundreds of thousands of dollars.
Considering the high volume of RFIs between construction and design teams, as well as multiple revisions of documents and limited time for adequate drawing coordination, our client understood the challenge of meeting the schedule and cost requirements. That’s when the need to implement technological solutions came into play.
Efficiency recognized by applying BIM technology
Though project teams work hard to identify clashes before construction begins, the breadth of information project members must account for is substantial and vulnerable to human error. Clash detection is one of the many downstream uses of a robust 3D model or building information model (BIM) and a valuable tool for identifying conflicts within the virtual design and construction (VDC) process.
Clash detection provides a unique perspective on the various disciplines that contribute to a working 3D project model. The process leverages numerous 3D models and data from varying disciplines, including architectural, structural, civil, process, and electrical to identify and resolve clashes before design is complete or construction begins. This helps maintain a high level of coordination between disciplines, stimulating important conversations earlier so conflicts can be identified and addressed as early as possible.
By partnering with ZELUS and using the power of clash detection software, our client was able to do just that. Providing BIM/VDC services, ZELUS assisted in lead coordination, with an emphasis on coordination with the shell and structural components of the facility. Highly accurate 3D models identified design and construction issues early in the processes, particularly clashes with structural elements, sprinklers, rigid ducts, and electrical panels. After just four weeks of coordination services, the 3D models helped reveal nearly 70 coordination issues.
The visibility and transparency BIM provided to all stakeholders was critical to avoiding misquotes on budget estimates, rework, and schedule delays that could have cost the project millions of dollars. It also allowed our client to get real-time feedback on proposed changes.
Project Highlights
- 650,000-square-foot inbound cross-dock facility
- Identify design/build issues early
- Particularly clashes with structural elements, sprinklers, rigid ducts, and electrical panels
- Coordination with material handling equipment and help fit efficiently into existing space being built
- 67 coordination issues were discovered after only 4 weeks of coordination services
Deliverables
- BIM/VDC Services
- Lead coordination (design coordination)
- Emphasis on coordination with the shell and structural components early in the construction process
- Lead coordination (design coordination)
- 3D modeling services
- Provided accurate and detailed fire protection model, streamlining the process of mechanical design, detailing, fabrication, and MEP installation
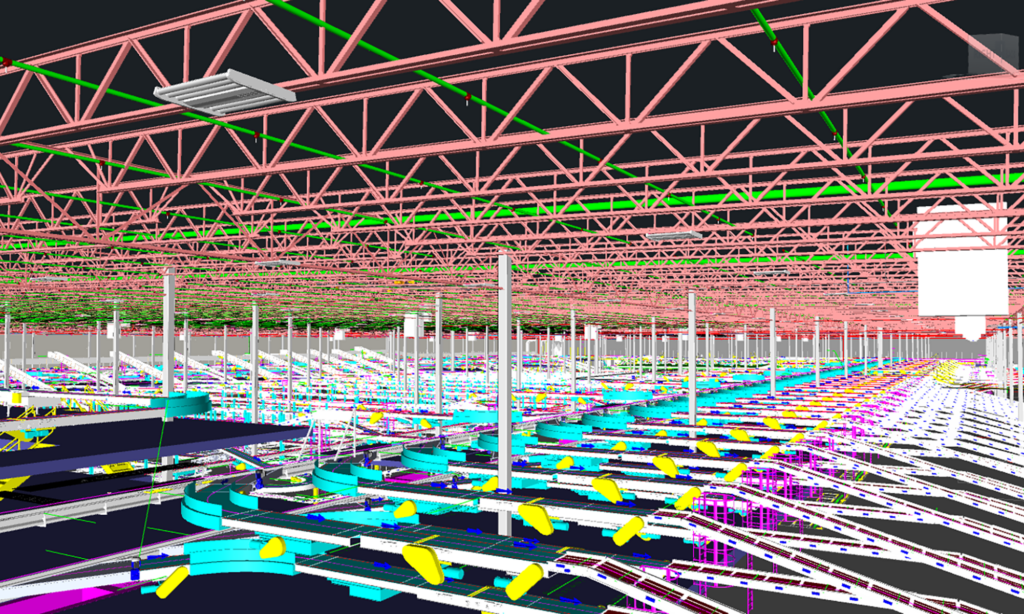
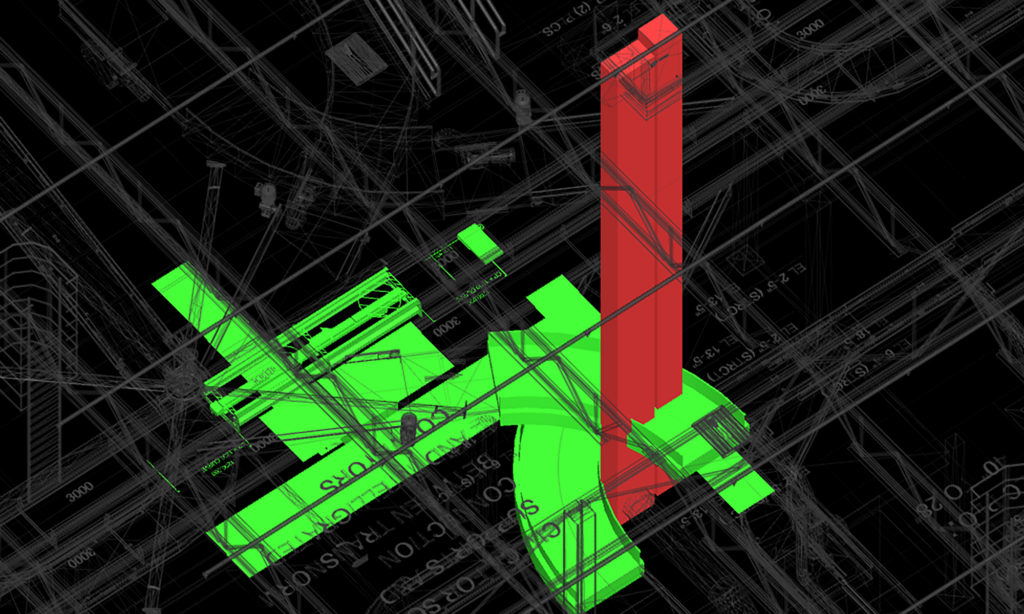

